デジタルツインによる工場のスマート化・活用事例|製造業の未来と課題とは
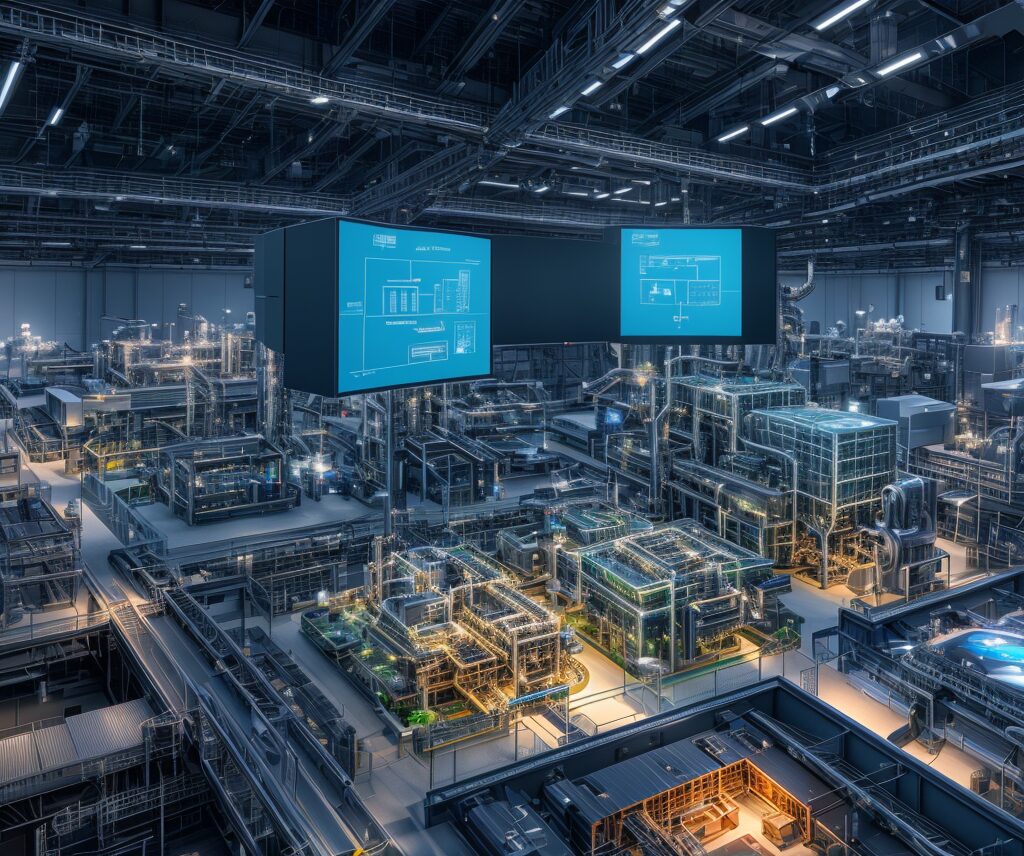
デジタルツイン技術は近年、製造業において大きな注目を集めています。
この技術は、仮想空間に現実の工場や製品を再現し、リアルタイムで現実空間を監視・管理することを可能にします。本記事では、デジタルツインの基本概念から製造業への具体的な活用事例までを詳しく解説します。
- 1. デジタルツインとは何か?製造業におけるデジタルツインの定義と、注目される理由
- 1.1. デジタルツインの基本概念
- 1.2. デジタルツインとメタバースの違い
- 2. 製造業へのデジタルツインの活用メリット
- 2.1. 1.リアルタイムデータ監視・分析による予知保全
- 2.2. 2.生産プロセスの最適化・効率化
- 2.3. 3.デジタルツインによる遠隔監視・支援による人手不足の解消
- 2.4. 4.製品の試作のコスト削減や工場のシミュレーション
- 3. 工場のデジタルツインの構築手順4ステップ
- 3.1. 1.既存のデータ管理や業務の課題の洗い出し及び目標設定と要件定義
- 3.2. 2.データ収集とインフラ整備
- 3.3. 3.デジタルツインの構築
- 3.4. 4.3Dシミュレータによるシステムの統合
- 3.5. 本番運用及び保守・メンテナンス
- 3.6. デジタルツインを実現する技術①IoT
- 3.7. デジタルツインを実現する技術②AI
- 3.8. デジタルツインを実現する技術③AR・VR・MR
- 3.9. デジタルツインを実現する技術④5G・ローカル5G
- 3.10. 工場のデジタルツイン化・XR活用を支援する企業
- 4. 製造業でのデジタルツイン活用事例
- 4.1. AGC社:化学品プラント工場をデジタルツイン化
- 4.2. ダイキンのデジタルツイン
- 4.3. 富士通の製造業向けデジタルツイン
- 4.4. デンソーの工場のデジタルツイン
- 4.5. 国土交通省のデジタルツイン「PLATEAU(プラトー)」
- 5. デジタルツインの課題や今後の展望
- 6. まとめ・更なる技術革新に向けて
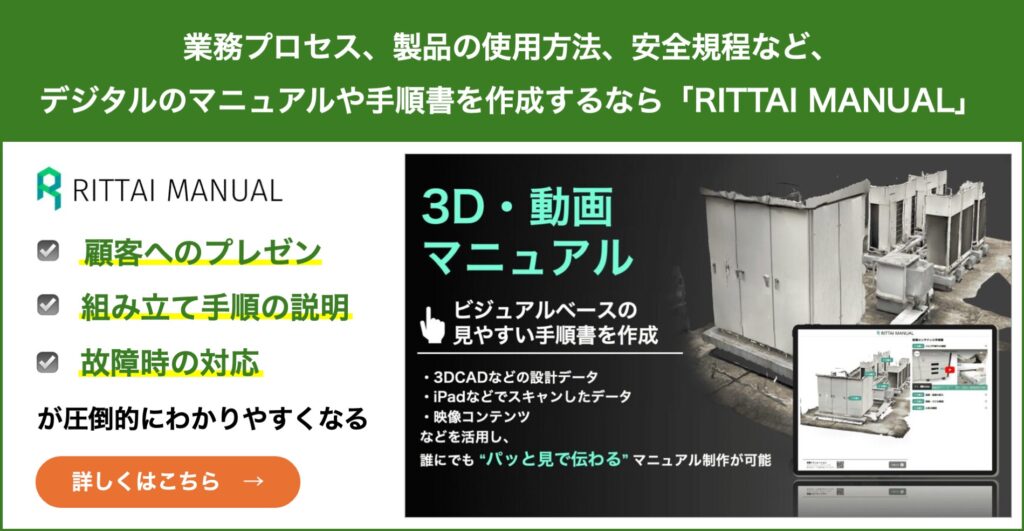
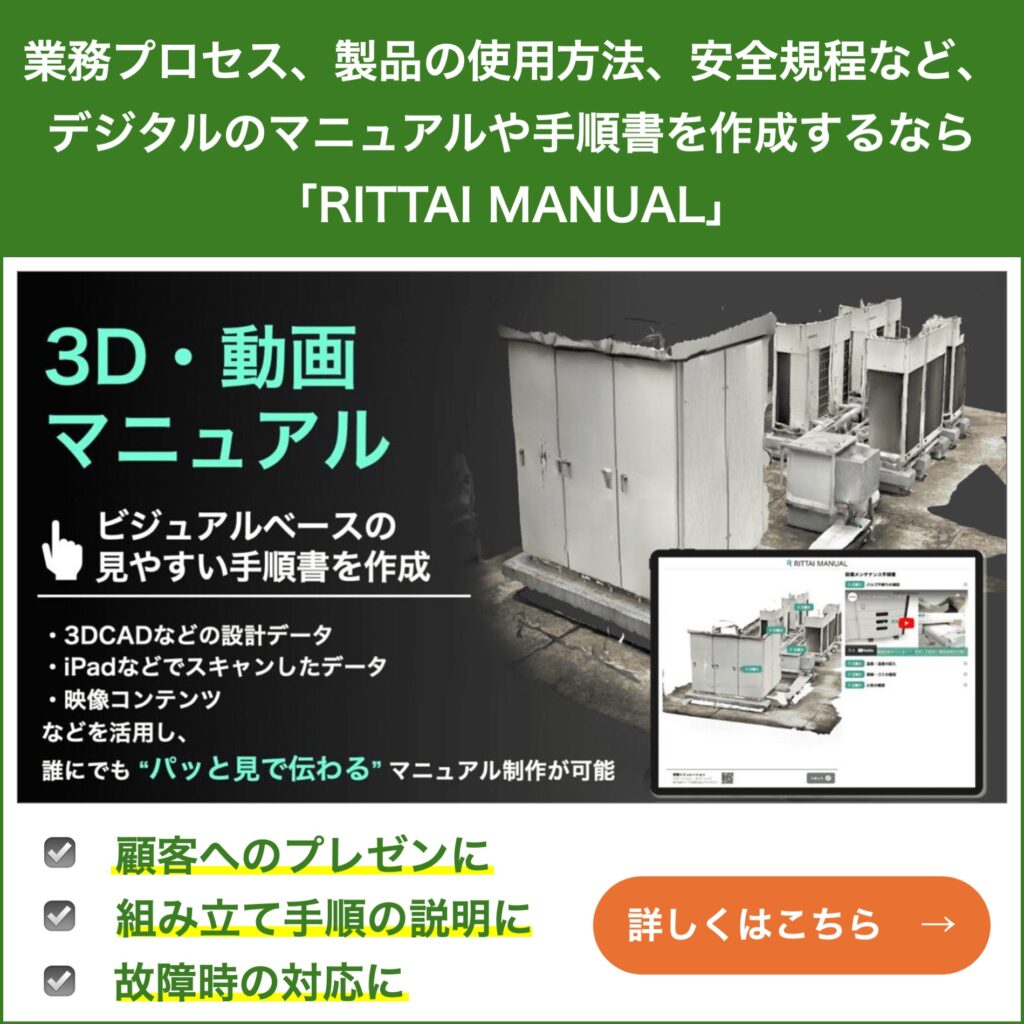
デジタルツインとは何か?製造業におけるデジタルツインの定義と、注目される理由
デジタルツインの基本概念
デジタルツインはその名の通り「現実空間をデジタル化したもの」を指します。
表面的なコピーではなく、状態・挙動などをリアルタイムでデジタル化しシミュレーションします。
製造業におけるデジタルツインは、製造プロセスや製品の物理的な構造、機能をデジタル上に再現することで、生産ラインの効率化や製品品質の向上を図るものです。
製造業では、生産設備や製品の設計データ、センサーデータを元にデジタルツインを構築し、製造過程をリアルタイムで監視、シミュレーションすることで、設備の稼働状況や製品の性能を最適化できます。
デジタルツインとメタバースの違い
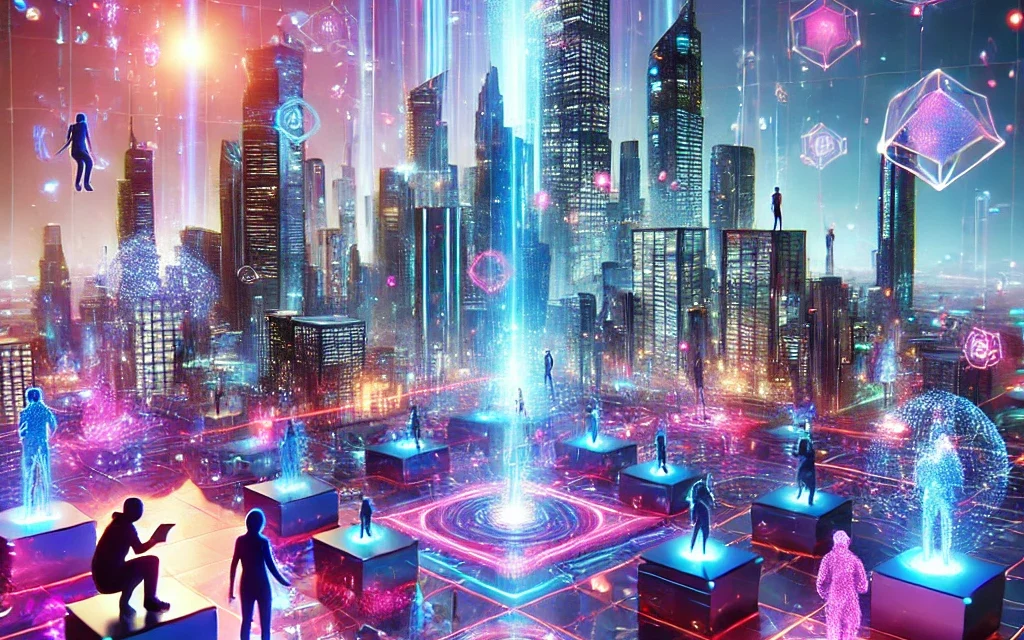
デジタルツインと近いワードとされる「メタバース」ですが、両者は若干異なります。その差異は、以下のように捉えられます。
- メタバース:完全な仮想空間。現実空間を模しているものもあれば、現実には存在しない仮想空間もある。また、複数人が同時に接続し、コミュニケーションを行える空間を指す。
- デジタルツイン:あくまで現実空間をリアルタイムでデジタル化したもの。複数人でのコミュニケーションは不要。
あくまでデジタルツインは現実空間のデジタル化に比重を置いており、産業用途での利用が主である一方で、メタバースは一般ユーザーをメインペルソナとしたコミュニケーションスペースという色合いが強いです。
製造業へのデジタルツインの活用メリット
デジタルツインは、製造業において様々なメリットをもたらすことから注目されています。
例えば、デジタルツインを活用することで、製品の設計段階から、工場での製造・運用・保守に至るまで、あらゆる段階で効率化や品質の向上を実現できます。また、製造現場の可視化やデータ分析にも役立ち、より効率的な生産計画や品質管理を可能にします。
なぜ今、デジタルツインが注目されるのか、その活用メリットを説明していきます。
1.リアルタイムデータ監視・分析による予知保全
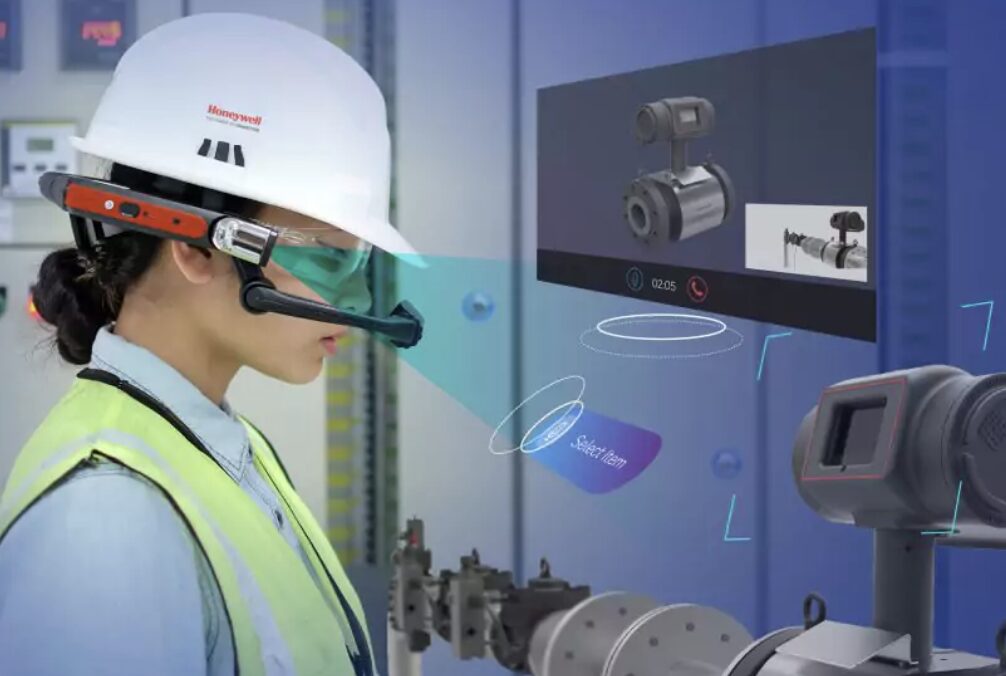
デジタルツインでは、工場内の各種設備の機器の状態をIoTデバイスから収集し、リアルタイムで監視し、過去のデータ分析に基づいて、機器の故障を予測することができます。
設備の稼働データをリアルタイムで分析し、パフォーマンス状況と、過去の可動・故障データなどを参照することで、わずかな変化もキャッチし、故障の兆候を検知し、事前にすることがメンテナンスが可能となります。
これにより、設備のダウンタイムを最小限に抑えることができます。
2.生産プロセスの最適化・効率化
デジタルツインを使用して生産ライン全体をシミュレーションし、生産効率の向上やエネルギー消費の削減が図れます。
例えば、ボーイングは、MarkLogicを基盤としたモデルベースシステムズエンジニアリング(MBSE)を導入し、デジタルツイン技術を活用して製造プロセスを効率化しています。
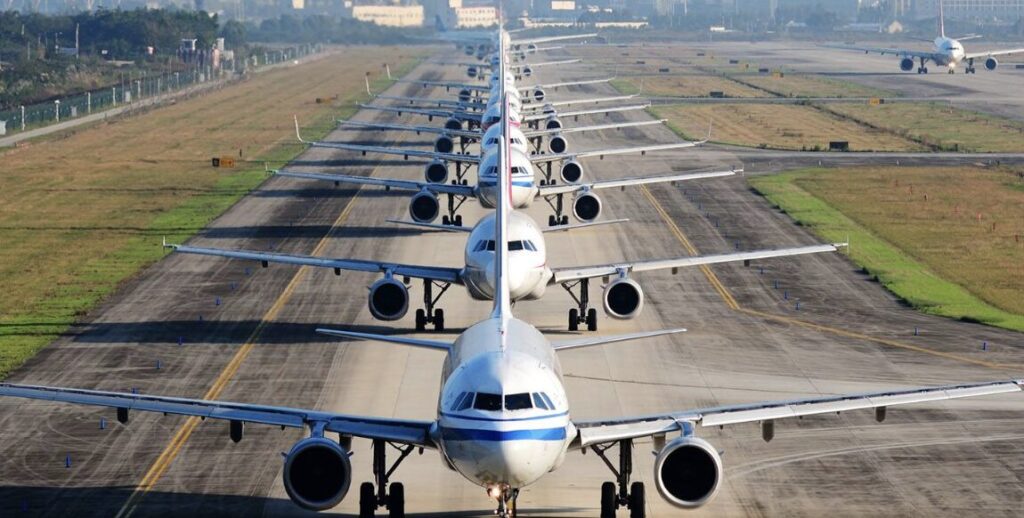
MBSEにより、製品開発におけるデータの統合とリアルタイムでの影響分析が可能になり、システム全体の理解が深まり、品質向上とコスト削減を実現しました。また、データの一貫性とセキュリティが強化され、複雑な製造工程の可視化が可能になっています。
参考記事:MarkLogicはボーイングのMBSEをどのように実現したか
3.デジタルツインによる遠隔監視・支援による人手不足の解消
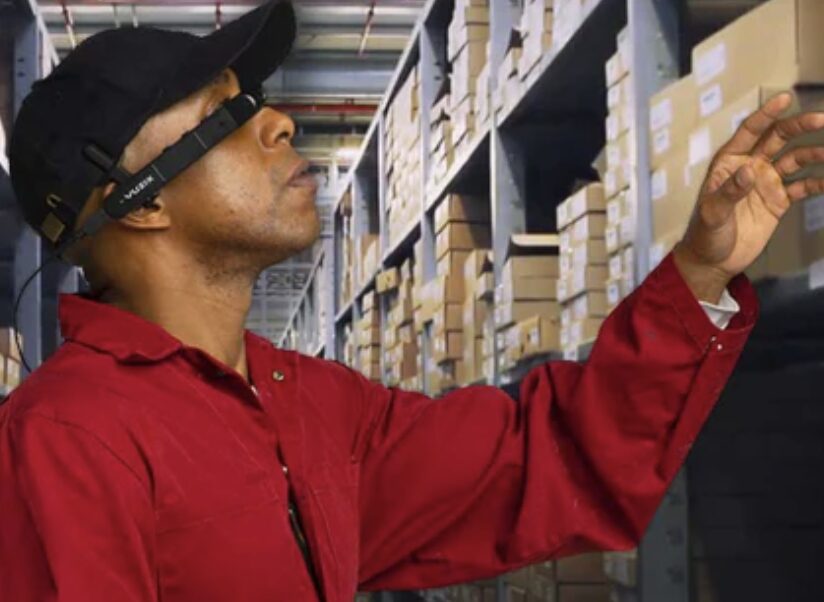
デジタルツインを用いると、遠隔地からでも工場や設備の状態をリアルタイムで監視したり、遠隔地からの設備や装置の操作や制御も可能にします。
また、遠隔の技術者は現場に赴くことなく工場や設備の状態を把握し、現地の作業員に必要な指示を出すこともできるため、人材不足や地理的な制約・移動時間といったを解消する効果も期待できます。
4.製品の試作のコスト削減や工場のシミュレーション
デジタルツインを活用することで、シミュレーションによって試作品の製造コストを削減できます。
近年、製造業では3DCADによる製品設計が主流となりつつあります。設備の3Dデータを組み合わせて製造ラインをデジタルツイン化し、仮想空間上で試作品の製造や検証も可能になります。
これにより、従来実際に設備を稼働させ、原材料から製造していた試作品も、ソフトウェア上で制作できるようになり、大幅なコスト削減を実現できます。
工場のデジタルツインの構築手順4ステップ
実際に工場をデジタルツイン化する場合、以下の4ステップが必要になります。
1.既存のデータ管理や業務の課題の洗い出し及び目標設定と要件定義
まず、デジタルツイン導入の目的を明確にします。
- 設備の稼働効率を向上させる
- 製品品質を改善する
- 設備の予知保全を実現する
といった具体的な目標を設定します。その後、その目標に基づき、必要なデータやシステム要件を定義します。
この際、定義された要件に基づいてセンサーやIoTデバイス、データ収集システムの選定が行われますが、既存の生産管理システム(MES)やERPシステムとの連携を考慮する必要があります。
2.データ収集とインフラ整備
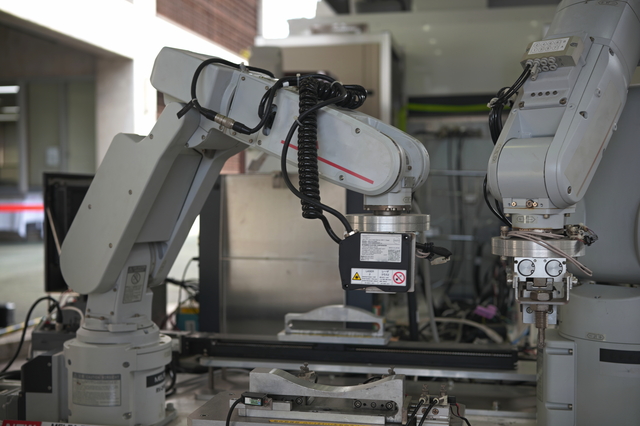
次に、工場内の設備や生産ラインにセンサーを設置し、必要なデータをリアルタイムで収集できるインフラを整備します。
これには、ネットワーク環境の構築やクラウドサービスの導入も含まれます。主に以下の内容となります。
- センサー設置:温度、圧力、振動など、モニタリングが必要なパラメータに応じて適切なセンサーを選定・設置します
- IoTプラットフォーム:収集したデータを一元管理するためのIoTプラットフォームを導入します。クラウドベースのプラットフォーム(例: AWS IoT、Azure IoT)やエッジコンピューティングを活用します。
- ネットワークインフラ:セキュアで高速なデータ伝送が可能なネットワークを構築します。5GやWi-Fi 6など最新の通信技術を利用することも考慮します。
3.デジタルツインの構築
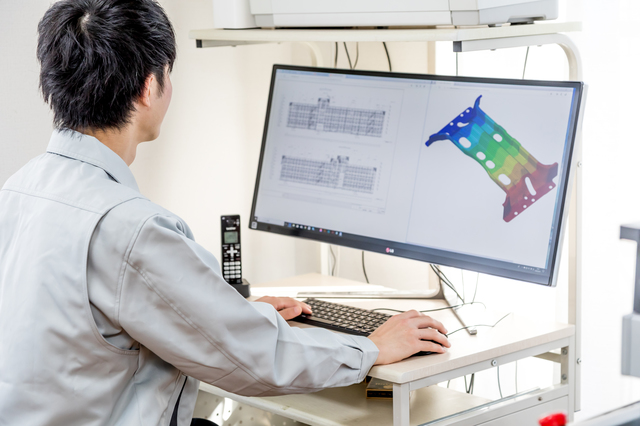
物理的な工場のモデルをデジタル上に構築します。
これには、CADデータを基に工場の生産ラインの3Dモデルを作成し、収集したリアルタイムデータを反映させるプロセスが含まれます。モデルには、機械やライン全体の物理的挙動や生産プロセスが再現されます。
具体的には以下の内容となります。
- 3Dモデリング:工場設備や生産ラインの詳細な3Dモデルを作成します。CADソフトウェア(例: Autodesk、SolidWorks)を使用します。
- シミュレーションエンジン:デジタルツインに基づいてシミュレーションを行うためのエンジン(例: SiemensのSimcenter、Ansys、UnrealEngineなど)を導入します。
- リアルタイムデータ連携:IoTプラットフォームから得られるデータを3Dモデルにリアルタイムで反映させるためのデータインテグレーション技術を活用します。
4.3Dシミュレータによるシステムの統合
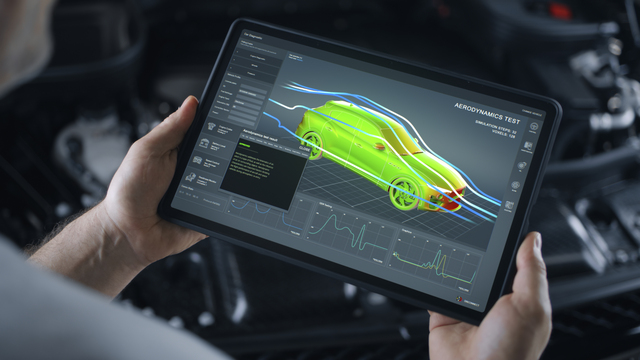
デジタルツインを稼働させるためのシステムを統合し、工場内の実際の環境でテストを行い、システムが期待通りに動作しているかを確認します。
- システムインテグレーション:生産管理システムやデジタルツインプラットフォーム、センサーシステムを一つに統合します。APIやカスタムインターフェースの開発が必要になる場合もあります。
- テストプロトコル:工場稼働をシミュレーションするためのテストプロトコルを開発し、異常が発生した場合の対応を検証します。
本番運用及び保守・メンテナンス
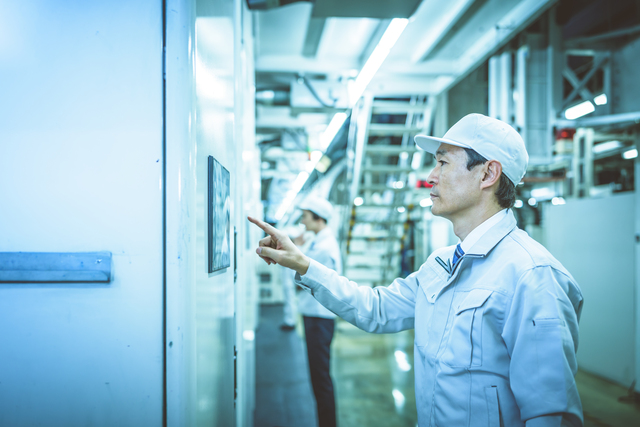
システムを本番稼働させ、デジタルツインを通じて工場の運用を最適化します。
リアルタイムデータの分析を基に、設備の稼働状況をモニタリングし、異常が発生した場合の対処やプロセスの最適化を継続的に行います。
例えば、以下の内容となります。
- データ管理・分析:収集されたデータを分析し、予兆保全やプロセスの最適化に活用します。AIや機械学習アルゴリズムを導入することが一般的です。
- ダッシュボードによるデータのビジュアライズ:運用状況をリアルタイムで監視するためのダッシュボードを開発・実装します。ビジュアルアナリティクスツール(例: Power BI、Tableau)を利用すると少ない工数でも実現可能です。
また、デジタルツインを維持し続けるためには、継続的なメンテナンスとデータの更新が必要です。特に、新しいデータや技術が導入された場合には、デジタルツインもアップデートする必要があります。
定期的にセンサーやシステムから取得されるデータを更新し最新に近いデジタルツインを保持したり、システムが外部からの攻撃に対して脆弱でないか、セキュリティ対策を定期的に確認し、アップデートします。
これらの段取りをしっかりと実行することで、デジタルツイン技術を工場に効果的に導入し、持続可能で効率的な運用を実現することが可能になります。
※大手化学メーカーなど多数のデジタルツインの実装支援実績のある会社はこちら
デジタルツインを実現する技術①IoT
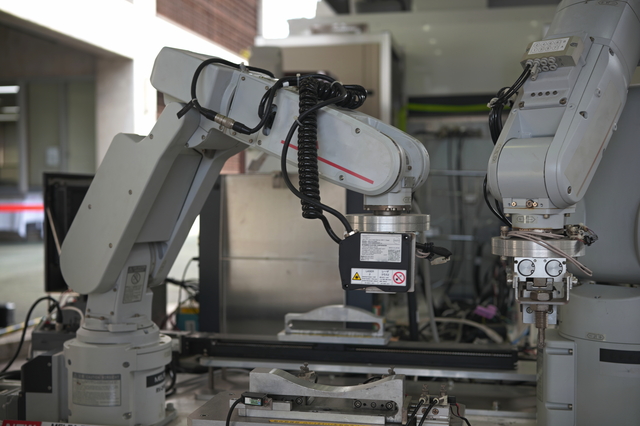
IoTデバイスは、工場内の各設備・インフラからデータを収集し、仮想空間に反映させる際に必要になります。
IoTデバイスは、センサーやアクチュエータなどのデバイスをネットワークで接続し、リアルタイムでデータを収集します。デジタルツインは、これらのIoTデバイスから収集されたデータを活用して、物理的なオブジェクトの状態を仮想空間上に再現します。
デジタルツインを実現する技術②AI
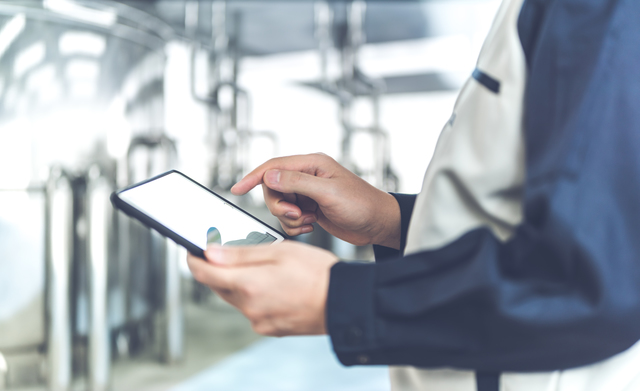
AIは、IoTデバイスから取得する大量のデータを分析し、パターンや傾向を検出する形で活用します。
こちらも、あくまで「デジタルツインから何を実現したいか」により活用方法やデータ設計は異なります。
実際の設備のパフォーマンスデータや、作業員による作業データを数値から分析したり、現地の画像データから画像認識AIにより作業内容の解析や正誤判定を行うなど、活用方法によりデータ取得やデータ蓄積を適切な形で設計しておく必要があります。
デジタルツインを実現する技術③AR・VR・MR
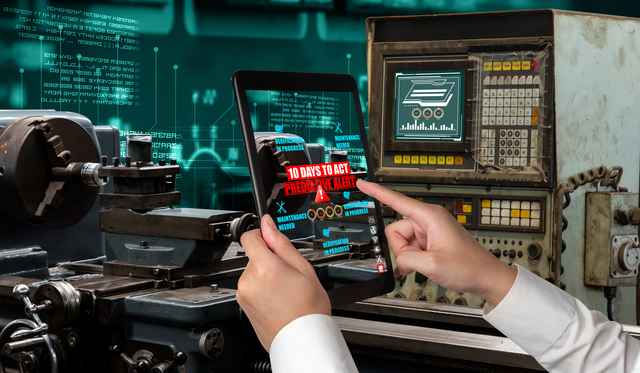
拡張現実(AR)や仮想現実(VR)の技術により、デジタルツインの視覚化が可能になります。
AR技術は、現実世界にデジタル情報を重ねて表示する技術です。VR技術は、仮想空間を体験できる技術です。
ARやVR技術を用いて、仮想空間上に再現されたオブジェクト(工場内の製造ライン・設備)や取得データを3Dでビジュアライズすることができます。これにより、ユーザーは、デジタルツインをより直感的に理解し、操作することができます。
製造業・工場におけるXR活用事例やポイントが気になる方はこちら:
- AR(拡張現実)やMR(複合現実)の活用事例・活用方法→【製造業・工場のAR/MR/VR活用事例】メリットや導入のポイントを解説
- VRの活用事例・活用方法→【2024年最新】製造業・工場のVR活用事例と導入プロセス・費用
デジタルツインを実現する技術④5G・ローカル5G
高速通信技術の5Gにより、リアルタイムでのデータ伝送が可能になります。
5Gは、従来の通信技術よりも高速で、低遅延な通信を実現する技術です。デジタルツインは、5Gを用いることで、リアルタイムで大量のデータを伝送することが可能になります。これにより、よりリアルタイムで正確なデジタルツインを実現することができます。
セキュアなデータ送信・管理を行いたい場合、ローカル5Gによりクローズドなネットワークを構築することでセキュリティを担保することができます。
工場のデジタルツイン化・XR活用を支援する企業
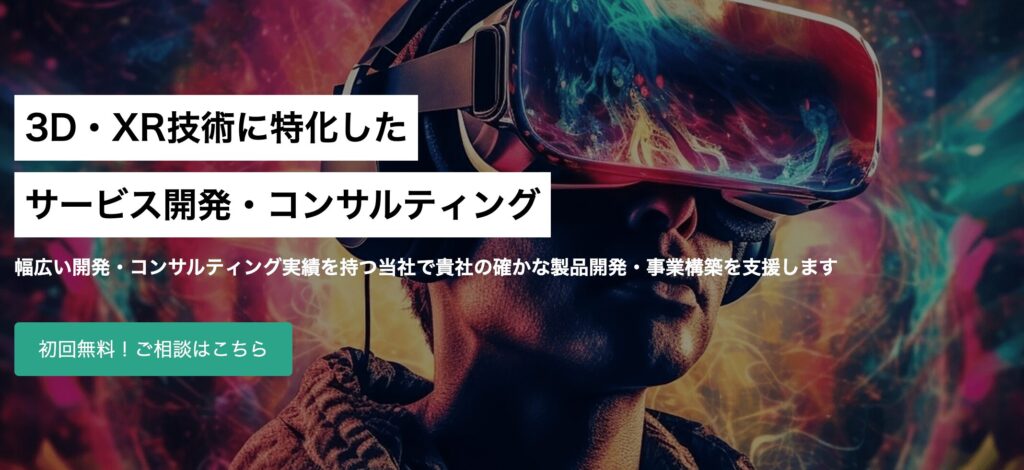
当メディアの運営元・株式会社Forgersは、製造・通信・小売業など幅広い業界の企業に対して、VR/ARやデジタルツインの実装・コンサルティング支援を行ってまいりました。
NTTドコモ、アイシン、ニトリ、NTT東日本などのXR開発や、大手化学メーカーの「工場のデジタルツイン化」も支援しています。
スマートファクトリーの実現や、工場のデジタルツインの実現に向けて、企画・設計のコンサルティングや3D/XR開発も行いますので、少しでもご興味がある方は、こちらからご相談ください。
製造業でのデジタルツイン活用事例
AGC社:化学品プラント工場をデジタルツイン化
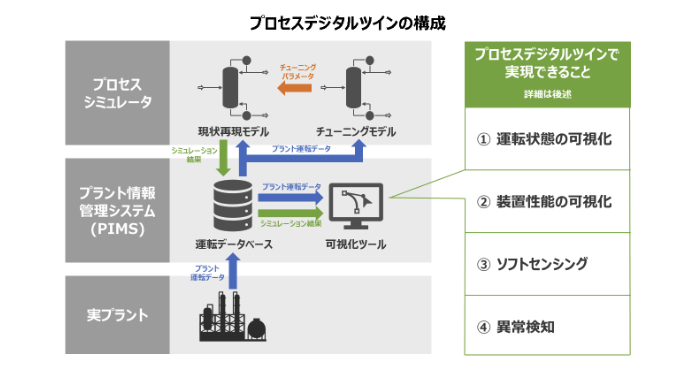
AGC社は、ガラス製造におけるデジタルツイン技術を活用し、カーボンニュートラルの実現に向けた新しい取り組みを進めています。
化学品プラント工場の運転データを取得し、デジタルツイン化。運転状態や装置性能などを可視製造プロセスのリアルタイムなシミュレーションや最適化が可能になり、エネルギー効率の向上と温室効果ガスの削減に貢献しています。
AGCはさらに、デジタルツイン技術を基盤とした新しい製造プロセスとして「溶融塩技術」の開発を進めています。この技術は、従来の石炭に依存したガラス製造方法を見直し、再生可能エネルギーを活用することで、温室効果ガスの排出を大幅に削減することを目指しています。デジタルツインにより、溶融塩技術の導入プロセス全体を精密にシミュレーションし、最適化することで、持続可能な製造体制を確立しようとしています。
これにより、AGCは製造業界において環境負荷を最小限に抑えながら、効率的で持続可能な生産活動を推進していくことを目指しており、業界全体のカーボンニュートラル化に向けたリーダーシップを発揮しています。
この技術革新により、持続可能なガラス製造を目指しています。
参考はこちら
ダイキンのデジタルツイン
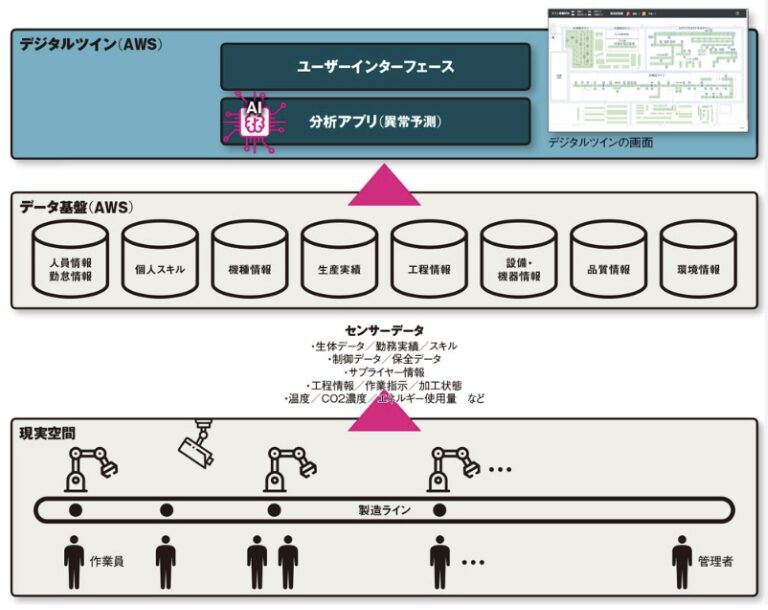
ダイキンは、2018年に空調機器の製造の生産管理にデジタルツインを導入し、生産プロセスの効率化と製品品質の向上を実現しています。
製造ライン上のIoTデバイスから取得したデータ(生成データ、制御データ、CO2濃度など)をリアルタイムで取得し、異常の事前予知・重大インシデントの防止に取り組んでいます。
参考記事はこちら
富士通の製造業向けデジタルツイン
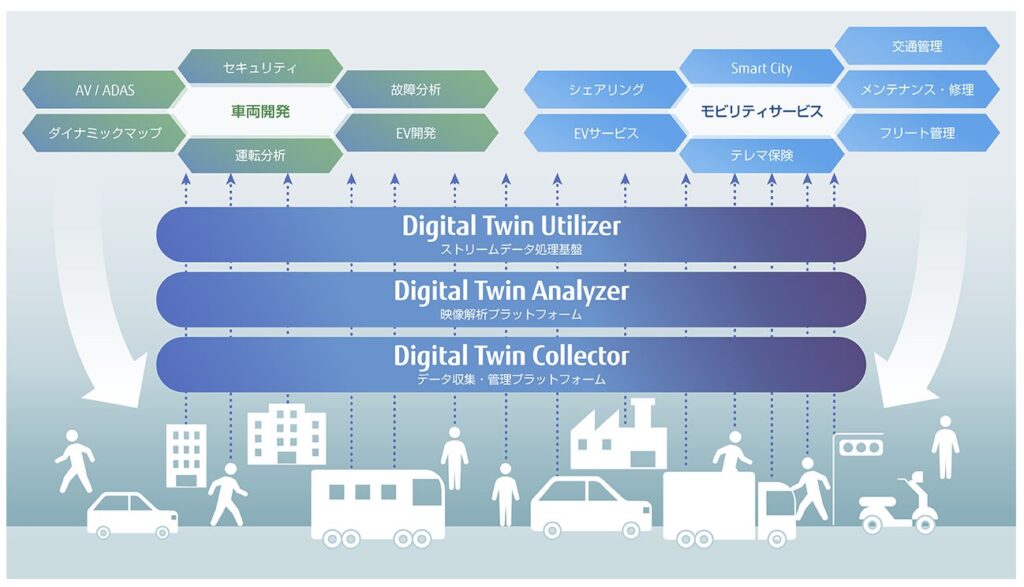
車両の設計、製造、運用、保守の各段階でデータを統合・分析することで、生産プロセスの効率化や製品品質の向上を実現します。
このソリューションは、車両ライフサイクル全体をシミュレーションし、コスト削減や開発期間の短縮を可能にし、自動車メーカーの競争力強化に寄与するサービスとなっています。
※詳細はこちら
デンソーの工場のデジタルツイン
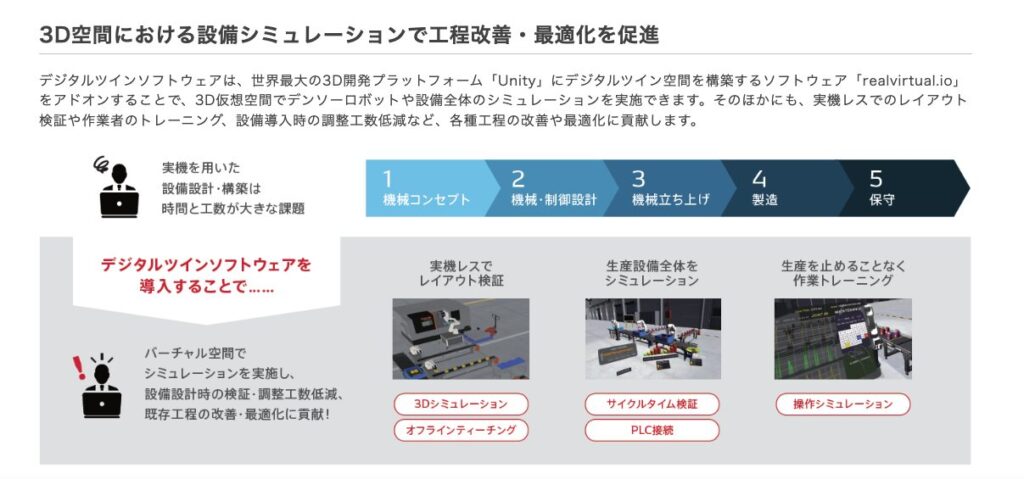
デンソーウェーブのデジタルツインシステム「DTS」は、工場の生産ラインを仮想空間上に再現することで、実際の生産プロセスをリアルタイムでシミュレーションし、最適化するためのソリューションです。
このシステムは、ロボットや設備の動作を正確にモデル化し、生産性の向上や設備の効率的な運用を支援します。また、トラブルの予測や対策を事前に行うことが可能で、工場全体の安定した稼働を実現します。
詳細はこちらでご確認ください。
国土交通省のデジタルツイン「PLATEAU(プラトー)」
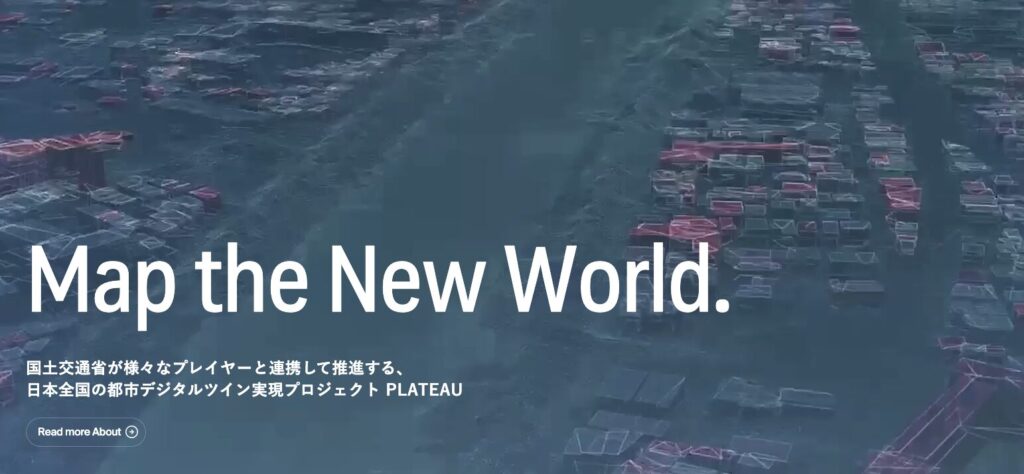
国土交通省が推進する「デジタルツイン・PLEATAU(プラトー)」は、都市の3Dデータを活用し、都市計画や防災対策などの分野でリアルタイムなシミュレーションを可能にするプラットフォームです。
このプラットフォームは、自治体や企業がデータを共有し、効率的な都市管理や新たなサービスの開発を支援することを目指しています。
- 詳細はこちら
デジタルツインの課題や今後の展望
デジタルツインの導入にはいくつかの課題があります。
例えば、デジタルツインを構築するために必要な膨大なデータの収集や管理、セキュリティ対策が挙げられます。また、実際のシステムとデジタルツインの精度を保つためには、継続的な更新と校正が必要です。
一方、日本国内ではセキュリティに対する考え方から、製造業における工場データの3D化やクラウド上への管理にハードルは大きいため、なかなか活用が進みづらいと言えます。
また、デジタルツインは工場全体のデータをシミュレーションするという背景から活用時には膨大なコンピュータエンジンが必要になり、導入にはハードウェアやクラウドの初期投資が必要となります。
よって、今後の発展には、クラウド上の情報漏洩・セキュリティ対策の強化や、シミュレーションの軽量化・ハードウェアの発展が不可欠と言えます。
まとめ・更なる技術革新に向けて
デジタルツインは製造業の未来を切り開く重要な技術であり、その活用が進むことで業界全体の革新が期待されます。
デジタルツインは、製造業の効率化、品質向上、コスト削減、持続可能性など、様々な課題解決に貢献する技術です。今後、デジタルツイン技術は、製造業だけでなく、様々な業界で活用されることが期待され、社会全体の進化に貢献していくでしょう。
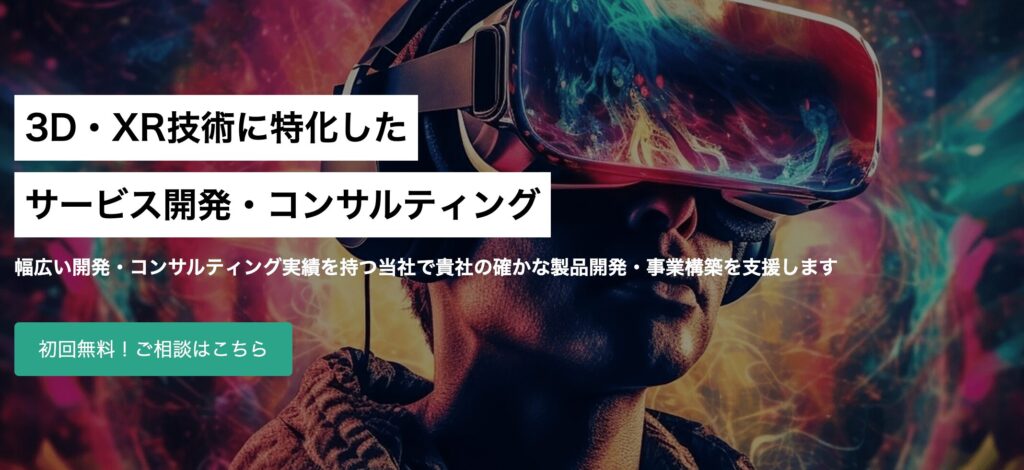
また、当メディアの運営元・株式会社Forgersは、製造・通信・小売業など幅広い業界の企業に対して、VR/ARやデジタルツインの実装・コンサルティング支援を行ってまいりました。
NTTドコモ、アイシン、ニトリ、NTT東日本などのXR開発や、大手化学メーカーの「工場のデジタルツイン化」も支援しており、スマートファクトリーの実現や、工場のデジタルツインの実現に向けて、企画・設計のコンサルティングや3D/XR開発も行います。
少しでもご興味がある方は、こちらからご相談ください。
関連記事: